!! ATTENTION !!
- | The welcome reception on October 22 will occur at Hiroshima Andersen, not the symposium venue. Please come directly to Hiroshima Andersen, where you can register for the symposium. The welcome reception starts from 18:00 to 19:30. |
- | October 23 and 24, you can register for the symposium at the International Conference Center Hiroshima, the symposium venue. |
- | -Participants for the JFPS HIROSHIMA 2024 are kindly invited to visit the Hiroshima Peace Memorial Museum. The admission fee will be waived upon presenting the symposium name card at the entrance on October 22nd-26th, 2024.
|
Program at a Glance
October 22 (Tue) |
October 23 (Wed) |
October 24 (Thu) |
October 25 (Fri) |
|
VENUE |
||||
Morning |
Invited lecture (Prof. Koichi SUZUMORI) Technical sessions |
Keynote speech (Dr. rer. nat. Steffen Haack) Keynote speech (Dr. Claudio Semini) Technical sessions |
||
Afternoon |
Invited lecture (Prof. Bing XU) Keynote speech (Mr. Charbel Nasr) Technical sessions |
Invited lecture (Prof. Terenziano RAPARELLI) Invited lecture (Prof. Toru YAMAMOTO) Technical sessions |
||
Evening |
Final Program
Final Program for the 12th JFPS International Symposium on Fluid Power, HIROSHIMA 2024
The symposium papers and presentation videos are available for those who registered for the symposium through the Final Program.
Regarding the online platform of JFPS2024 HIROSHIMA, login information has been announced to those who registered for the symposium by e-mail.
Invited Lecture
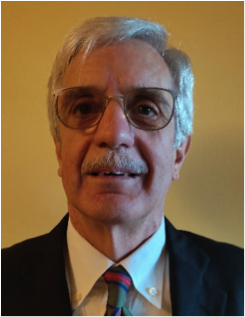
"Some Recent Research Results in Air Bearings and Pneumatic Components at Italian Universities"
13:30-14:10 on October 24 @Room A (Himawari)
Professor Terenziano RAPARELLI
Politecnico di Torino, Italy
Prof. Terenziano Raparelli is full professor in Applied Mechanics and Fluid Automation at the Department of Mechanical and Aerospace Engineering (DIMEAS) of the Politecnico di Torino, Italy, where he received his MS degree in Mechanical Engineering in 1981 and, since that time he worked first as a researcher an then as professor, with a parenthesis, 1994-1999, at the University of L’Aquila, Italy. He is currently Head of the Gas Bearings Laboratory at DIMEAS. He was Coordinator of the Board of Mechanical, Aerospace, Automotive and Production Engineering of the Politecnico di Torino and he is fellow member of the following scientific associations: International Federation for the Theory of Machines and Mechanisms (IFToMM), Italian Association of Theoretical and Applied Mechanics (AIMETA), Italian Association of Tribology (AIT).
His major research areas of interest are pneumatics, tribology, robotics, bioengineering, gas bearings. Relatively to these areas he has written several papers and, moreover, textbooks on Applied Mechanics and Pneumatics.
Abstract: In various industrial sectors there are increasingly frequent signs of support for eco-sustainable technologies. Air bearing technology is one of these technologies, as it combines the eco-compatibility needs of the components with the technical needs to be able to operate at very high rotation speed, or with high handling precision. Both of these needs can be met thanks to the low viscosity of the air used as a lubricant between the moving surfaces.
As regards rotary applications, air bearings are used in high-speed compressors, small-sized turbomachines and electrospindles. As regards precision applications, air bearings are used in the metrology sector and in general in micro positioning.
Another interesting and growing sector is the collaborative robotics, that was born to increase human–machine collaboration in industrial and other environments. Hence, safety is the first requirement for human–robot interaction. Soft graspers and actuators reduce the risk of hazards and injuries. In order to handle objects of different shapes, sizes and needs, pneumatic soft graspers and actuators, also inspired by the biological world, have been developed. Their common characteristic of being made of soft material whose stiffness is not uniformly distributed.
This lecture presents some prototypes of air bearings, for high-speed applications and in the metrology sector, developed at the Department of Mechanical and Aerospace Engineering of the Politecnico di Torino. Some prototypes of pneumatic soft graspers and actuators, in some cases inspired by the animal world, designed and developed at the University of L’Aquila, are also presented in this lecture.
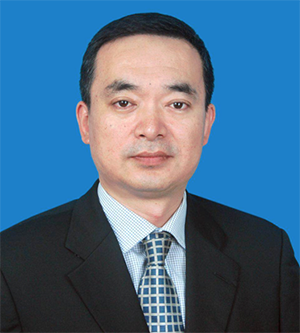
"Recent Hydraulic Fluid Power Research Activities in Zhejiang University"
13:00-13:40 on October 23 @Room A (Himawari)
Professor Bing XU
Zhejiang University, P. R. China
Bing Xu received his B.S., M.S., and Ph.D. degrees in mechanical engineering from Zhejiang University, P. R. China, in 1992, 1995, and 2001, respectively. After 3 years industrial experience as an chief technical engineer of an elevator hydraulic system company, he goes back to Zhejiang University until now. Now He is Executive Director of School of Mechanical Engineering and State Key Laboratory of Fluid Power and Mechatronics System in Zhejiang University. There are nearly 120 associates and more than 1200 graduate students (half of them is PhD students) in School of Mechanical Engineering. And Fluid Power Laboratory has 20 associates and nearly 200 graduate students.
He got his nomination of professorship in 2007, and his main research interests are Hydraulic piston components and mobile hydraulic system. He had published over 200 technical journal papers and conference papers, and granted more than 50 patents. He is the Director of China Hydraulic and Pneumatic Standardization Committee(SAC TC3)and Convener of WG1 of ISO TC131 SC8. Also he is Vice Director of Fluid Power Transmission and Control Institute(FPTCI) of China Mechanical Engineering Society(CMES). He is also the Board of Directors of Global Fluid Power Society (GFPS) and vice president of IFToMM China.
Abstract: Due to the impact of the COVID-19 epidemic, scholars and experts in the international fluid power academic community have not visited the Fluid Power Laboratory of Zhejiang University for many years. During this period, the research direction and content of the laboratory also have many new changes. At the end of 2022, the Fluid Power Laboratory of Zhejiang University had moved from the old Yuquan campus to the new Zijingang campus. Now the laboratory area has increased to 4000m2 and many new test rigs have been added.
The 11th Hangzhou International Conference on Fluid Power (ICFP2025) will be held in Hangzhou in April 2025, and the 40th anniversary of the ICFP Hangzhou International Conference (from 1985- 2025) will also be celebrated. Taking this opportunity, this lecture will briefly report on several important research projects in Fluid Power Laboratory of Zhejiang University in recent years, including hydraulic components tribology, ICT technology for hydraulic components, lightweight components (including non-metallic material substitution, additive manufacturing, and EHA integrated actuators), and control of heavy-duty hydraulic robotic arms, etc.
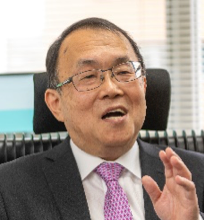
"Design of Data-Driven PID Controllers and Their Applications for a Hydraulic Excavator"
14:20-15:00 on October 24 @Room A (Himawari)
Professor Toru YAMAMOTO
Hiroshima University, Japan
Toru Yamamoto is currently a Professor with the Control Systems Engineering, Hiroshima University, Japan, and a leader of the National Project on Regional Industry Innovation with support from the Cabinet Office, Goverment of Japan. He was an Overseas Research Fellow of the Japan Society for Promotion of Science (JSPS) with the Department of Chemical and Materials Engineering, University of Alberta for six months in 2006. His current research interests are in area of self-tuning & learning control, data-driven control, and their implementation for industrial systems. Dr. Yamamoto was a General Chair of SICE (Society of Instrument and Control Engineers in Japan) Annual Conference 2019 held in Hiroshima. He received the Commendation for Science and Technology by the Minister of Education, Culture, Sports, Science and Technology, as well as the Technology Achievement Award from the Japan Society of Mechanical Engineers(JSME) and the Performance Award from the Institute of Electrical Engineers of Japan(IEEJ).
Abstract: In the industrial words, intensified international competition has led to increased emphasis on enhancing productivity, energy conservation, labor-saving measures, and improving product quality while reducing production costs. To address these issues, there is a growing demand for constructing advanced control systems. Particularly, recent advancements in computer technology enable rapid processing of vast amounts of data. This situation facilitates relatively straightforward accumulation, processing of operating data, and programming, leading to intensified efforts to enhance control performance. This trend has gradually altered the framework of control system design, with a recent focus on data-driven design methods that directly utilize operating data for control system design without describing mathematical models of the system.
Meanwhile, PID control methods are widely applied in the industries, reportedly constituting over 80% of all control loops. Given this current situation, methods for designing data-driven PID controllers are introduced in this talk. One method involves adjusting PID parameters directly from pre-collected operating data for linear systems, known as Fictitious Reference Iterative Tuning (FRIT). Another is the database-driven PID (DD-PID) control method which has been proposed for nonlinear systems. Initially proposed for online adjustment of PID parameters, this method has been extended to offline adjustment, in which databases is trained by using the FRIT. This extension significantly contributes to the societal implementation of the DD-PID method. Finally, the application results employing these methods to a hydraulic excavator are discussed.
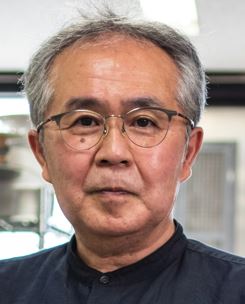
"Fluid Power Pioneering New Robotics"
9:20-10:00 on October 23 @Room A (Himawari)
Professor Koichi SUZUMORI
Tokyo Institute of Technology, Japan
Koichi Suzumori received the B.S., M.S., and Ph.D. degrees in mechanical engineering from Yokohama National University, Japan, in 1982, 1984, and 1990, respectively. He had worked for Toshiba R&D Center from 1984 to 2001, and worked for Micro-Machine Center, Tokyo, from 1999 to 2001. He had been a professor in Division of Industrial Innovation Sciences, Okayama University, Japan from 2001 to 2014. Since 2014 till present, he has been a professor in Department of Mechanical Engineering, Tokyo Institute of Technology. He is mainly engaging in the research fields of new actuators and their applications. He is a fellow member of the Japan Society of Mechanical Engineers and of the Robotics Society of Japan.
Abstract: Robotics started with fluid actuators in year 1960’s where most of the robotic systems apply hydraulic actuators including the first industrial robots, Unimate and Versatran from USA in year 1962. The first humanoid robot developed by Waseda University in the year 1970 was also driven by hydraulic actuators. Apparently, the first wearable robot was developed and driven by pneumatic McKibben muscles in year 1960. From there, development of robots using hydraulic and pneumatic were expanding significantly until 1980’s where high performance electrical motors were introduced. Consequently, since then, the fluid power actuators are categorized as conventional actuators and seldom used in robotics today.
However, fluid powered actuators are NOT too old to be used in current robots because it has a great potential for pioneering a new world of robotics. I will talk about it and show the following examples of fluid actuators and their applications in new concept of robotics. One of them is the "Pneumatic thin artificial muscle" which opens a new area of Musculoskeletal robotics, Giacometti robotics, Soft robotics, Power-assist wears, and deep biomimetic robotics. Our "Next-generation hydraulic actuator” with advantage of lightness, compactness, and fine controllability is possible for tough robotics to work in hazard conditions, rescue robotics, and soft high power robotics. I want to share these great potentials of the new fluid power systems in robotics with all participants.
Keynote Speech
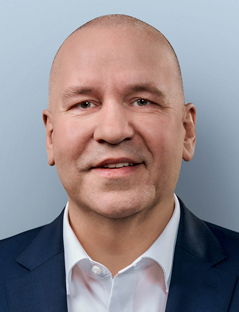
"Improving the productivity and sustainability of industrial and mobile fluid power systems through software and data utilization"
9:00-9:30 on October 24 @Room A (Himawari)
Dr. rer. nat. Steffen Haack
President of the Executive Board of Bosch Rexroth AG
Since January 2021 he has been a Member of the Executive Board of Bosch Rexroth AG with responsibility for the company’s entire development activities and the New Business product area. From 2017 to 2021, Steffen Haack has headed the Business Unit Industrial Hydraulics, having previously been a member of the Executive Board with responsibility for the Business Unit Industrial Applications from 2015 to 2017. From 2012 to 2014, Steffen Haack was a member of the Executive Board / President of the Executive Board of Bosch Solar Energy AG. The focus of his activities was the termination of all activities of the Bosch Group in the field of photovoltaics. From 2010 to 2012, he was responsible for Sales Factory Automation in the Business Unit Industrial Applications of Bosch Rexroth AG. The technology focus was on linear and assembly technology, electric drives and controls, including tightening and welding technology and pneumatics. From 2008 to 2010, he assumed responsibility for the Electric Drives and Controls Division of Bosch Rexroth AG.
Haack studied mechanical engineering at the University of Applied Sciences and completed a teacher training course for technology at the University of Erfurt. There in 1991, he gained a PhD (Dr. rer. nat.) in fluid technology at the faculty of mathematics and natural sciences. In 1996, he joined the Bosch Group. He then held various positions within the Bosch Group. In addition to his professional activities, Dr. Steffen Haack is President of the Executive Board of the Fluid Power Association of the German Engineering Federation (VDMA) and of the Advisory Board of the German Mechanical Engineering Summit.
Abstract: Based on the requirements of machine builders and operators, new possibilities for improving productivity and sustainability using software and data are identified for both industrial and mobile applications. In the industrial section the disadvantages of the hierarchical and proprietary automation pyramid are identified, and the future architecture based on RAMI 4.0 is described. The topics of administration shell, standardization and digital product twin are discussed in more detail. The challenges facing fluid technology are described: Setting up data factories to develop the administration shell, the product carbon footprint, the digital name plate, and the digital Product Passport. The possibilities and advantages of software-based hydraulics at product and system level are then demonstrated. The basis for this is the transfer of technology functions and fluid-mechanical variance through software modules. An entire digital ecosystem H4U for industrial hydraulics based on software apps will be presented and the benefits for machine builders and end users will be worked out. The software control and data technology implementation are then discussed using a proportional valve and a state-of-the-art hydraulic unit, and new business models are discussed.
In the mobile section the disadvantages of the today’s CAN architecture are identified, and the future architecture is described. This applies to both machine builders and end users on large construction sites. The challenges in mobile hydraulics are like the industrial ones: Setting up data factories to develop the administration shell, the product carbon footprint, the digital name plate, and the digital Product Passport. The possibilities and advantages of software-based hydraulics at product and system level are then demonstrated. The basis for this is the transfer of technology functions and fluid-mechanical variance through software modules. An entire digital ecosystem BODAS for mobile hydraulics based on software solutions will be presented and the benefits for machine builders and end users will be worked out. The software control and data technology implementation are then discussed using an eOC Axial Piston Pump and a state-of-the-art assistance machine function, and new business models are discussed.
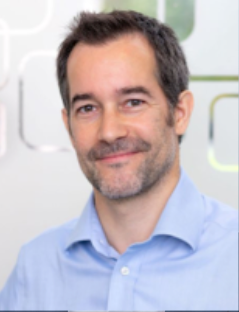
"Hydraulically Actuated Quadruped Robots for Automation in Rough Terrain Environments"
10:40-11:10 on October 24 @Room A (Himawari)
Dr. Claudio Semini
Istituto Italiano di Tecnologia, Italy
Dr. Claudio Semini (MSc 2005, PhD 2010) is the head of the Dynamic Legged Systems (DLS) lab at Istituto Italiano di Tecnologia (IIT) that developed a number of high-performance hydraulic robots, including HyQ, HyQ2Max, and HyQReal. He holds an MSc degree from ETH Zurich in electrical engineering and information technology. He spent 2 years in Tokyo for his research: MSc thesis at the Hirose Lab at Tokyo Tech and staff engineer at the Toshiba R&D center in Kawasaki working on mobile service robotics. During his PhD and subsequent PostDoc at IIT, he developed the quadruped robot HyQ and worked on its control. Since 2012 he leads the DLS lab.
Abstract: In this talk I will present an overview of 17 years of research and development of hydraulic quadruped robots and their locomotion control at IIT. First, I will give a quick chronological overview of the various hydraulic quadruped robot versions developed in IIT’s Dynamic Legged Systems lab. Next, I will focus on the most recent 140kg hydraulic HyQReal robot and explain in detail the various components of its compact hydraulic actuation system. The onboard hydraulic system consists of two compact hydraulic pump units that include filtration, heat management and smart pressure control. The components of the robot’s 12 rotary and linear actuators were mostly developed by our industrial partner MOOG, using Formula1 servo valves and additively manufactured parts in titanium for compactness and smart fluid routing. The servo valves allow the implementation of high-performance force and torque control that enables active impedance control. To conclude, I will present the results of some ongoing/recent projects in the fields of agriculture, space, and disaster response. The VINUM project focuses on the automation of winter pruning in vineyards with quadruped robots. The ESA-funded project ANT is about legged rovers for space exploration. And the INAIL-RT2 project is about a teleoperated legged manipulation platform for disaster response in rough terrain environments.
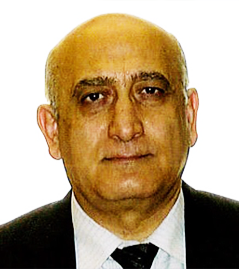
"Machine Knowledge Management: Essential Ingredient For Increased Productivity And Reduced Time To Market"
15:20-15:50 on October 23 @Room A (Himawari)
Mr. Charbel Nasr
President, Famic Technologies Inc., Canada
Mr. Charbel Nasr holds a Bachelor’s degree and Masters’ degree in Mathematics and Computer Science from the Université de Sherbrooke, Quebec, Canada. After a short career as a lecturer at the Université du Québec in Hull, he worked for the Ministry of Indian Affairs Canada as Manager of IT, Security and Technical Support. He then moved to Famic Technologies to manage the company as president since its beginning more than 35 years ago. Mr. Nasr is involved in the management, and the management of all R&D activities of many world-renowned software solutions the company offers.
Abstract: Across the wide spectrum of fields in the industry, all organizations have universally pursued common objectives of increasing productivity while trying to reduce time to market, albeit with varying degrees of success. As traditional non-integrated approaches have been proven inadequate due to lack of reusability of the work and content throughout the lifecycle of a machine, a substantial shift is needed to upend these conventional work processes and introduce a new methodology based on effective machine knowledge management, starting from the initial conception of the idea, all through prototyping, design, optimization, production and commissioning. The same need can be extended to the maintainability of the system in the field. This integrated approach preserves and leverages the knowledge created and accumulated from one phase to another throughout the entire life cycle of the machine, allowing for a seamless transfer between all stakeholders, eliminating rework and redundancy, accelerating innovation, and improving the overall efficiency of the process. The reusability of work from one phase to another, through a universal approach, favors synergy and communication between all the different stakeholders, and optimizes the work processes. This can also facilitate the transfer of knowledge between generations of workers. Production tools used must be trade-oriented, adapting to the users, instead of the opposite.
Welcome reception
The welcome reception will take place at Hiroshima Andersen on October 22nd from 18:00 to 19:30. The participants who have registered for the symposium can come directly to Hiroshima Andersen. The registration desk opens at Hiroshima Andersen from 16:00 to 19:00.
Note that no reception desk opens at the International Convention Center Hiroshima on October 22nd.
Banquet
HIROSHIMA 2024 offers a special occasion for the participants to join a banquet at Hiroshima Gokoku Shrine on the grounds of Hiroshima Castle on the evening of October 24th. This exceptional experience has been made possible by the special support of the Japan Tourism Agency. Don’t miss it!
For more information, please visit here.
Technical tour
Two technical tours are parallelly scheduled for October 25th. A participant can apply for either one or the other. Participating fee will be charged. Note that the tour will be canceled if there are 24 or fewer participants.
You can find a tour itinerary here.